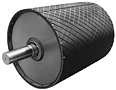
Bolt-On Replaceable Rim Lagging™
Benefits:
• Fits all standard manufacturers’ crown face drum pulleys
• RRL® comes in engineered pre-sized sets of 2 to 5 sections
– Crown face standard
– Saves up to 70% on labor
– Fewer sections, less welds, more belt to pulley contact
– No layout necessary
– No cutting necessary
• Order Bolt-On RRL® with a new pulley and Douglas will install it free of labor charge
• Reduce conveyor downtime and pulley installation/removal cost
• Ideally suited for severe applications
• Heavy steel backing plate with rolled in crown and truck tire tough 1/2" SBR/Natural rubber revitalizes old pulleys and adds years of service life
• Improve traction capacity of any pulley with Douglas Bolt-On RRL®
• Easy-on easy-off principle means that Douglas RRL® may be installed in the field without removing the pulley or the conveyor belt
• Minimum gap between segments means unequaled belt to pulley contact and more traction
Construction:
• All standard lagging is hot vulcanized in our plant to strict tolerances and the highest industry standards
• Diamond groove standard
Options:
• Optional Herringbone/Chevron groove or plain wrap cloth impression available
• Available in the same range of materials as Douglas conveyor pulley lagging
• Available with stainless steel backing plate

Ceramic Pulley Lagging™
Douglas® Ceramic Pulley Lagging delivers substantially increased traction over conventional pulley lagging. Durable ceramic tiles last longer than standard rubber lagging resulting in a dramatic reduction in the number of times the pulley must be changed over the life of the conveyor system. Douglas® Ceramic Pulley Lagging is constructed of the highest quality materials available and to the highest quality standards in the industry. The unique cross hatched feature of our square ceramic tiles helps to ensure tile retention and virtually eliminates tile loss during the critical initial break in period of the lagging.
Benefits:
• As much as twice the coefficient of friction over non lagged pulleys
• As much as 50% higher coefficient of friction over standard rubber lagging
• Virtually eliminates belt slippage
• Lower belt tension and less take-up weight increases life of components and belt
• Improves belt tracking
• Easily sheds water and dirt
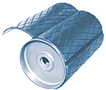
Replaceable Rim Lagging™
Patented Replaceable Rim Lagging™ (RRL™) is an innovative way to cover new pulleys and recover old pulleys. Engineered sections are made for specific pulleys and effectively cover the pulley face in a protective shell of rubber and steel and are an ideal way to save money and time. Can be installed on new pulleys in our plant or on the pulley in the field.
Benefits:
• Saves up to 70% on labor costs compared to other styles of replaceable lagging
• No layout necessary to fit to existing pulleys
• No cutting necessary: eliminates waste and scrap pieces
• Reduces conveyor downtime and reduces costs associated with pulley installation and removal
• Easy on/Easy off principle means Douglas® RRL™ may be installed in the field without removing the pulley or the conveyor belt
• Minimum gap between sections means the highest possible level of belt to pulley contact and results in a higher level of traction
• Order RRL™ with any new Douglas® pulley and we will install it for free
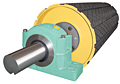
Sectional Retainer Lagging™
Douglas® Sectional Retainer Lagging (SRL™) delivers increased traction over non lagged pulleys. Increased traction between the pulley face and the belt bottom covers reduces belt slippage and helps to improve belt tracking. Double Chevron Grooves help shed water and dirt. Vulcanized rubber lagging protects the pulley’s face from wear and extends pulley service life. Can be installed on new pulleys in our plant or on the pulley in the field.
Douglas® Sectional Retainer Lagging is constructed of the highest quality materials available and to the highest quality standards in the industry. All sections are vulcanized in house using state of the art computer controlled autoclaves. Standard pulley lagging is a 60-65 Durometer Shore A SBR compound suitable for a wide variety of applications. Flat face is standard for SRL™. Special materials similar to the list of materials shown under Vulcanized Pulley Lagging and stainless steel backing plates are available.
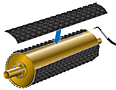
Tack-Lag Head Pulley Lagging
Benefits:
• A long lasting, low cost method of lagging and repairing your head pulley on site.
• One size pad fits all pulleys.
• Field cuts to any pulley length.
• No wasted material.
• Spot welds pads 3/4" apart for the perfect fit.
/Asset/flexible_tack_lag.jpg
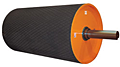
Vulcanized Pulley Lagging
Douglas® Truck Tire Tuff™ Conveyor Pulley Lagging delivers increased traction and pulley life over non lagged pulleys. Increased traction between the pulley face and the belt bottom covers reduces belt slippage and helps to improve belt tracking. Vulcanized rubber lagging protects the pulley’s face from wear and extends pulley service life.
Douglas® Vulcanized Rubber Pulley Lagging is constructed of the highest quality materials available and to the highest quality standards in the industry. All pulleys are vulcanized in house using state of the art computer controlled autoclaves and our patented bonding process. If you have an application that requires exact concentricity or T.I.R. we suggest ordering machined lagging with the tolerance specified. For some applications the initial cost will be quickly offset by labor savings when attempting start-up.
Benefits:
• As much as 50% increase in coefficient of friction over non lagged pulleys
• Improves Belt Tracking
• Protects pulley face from wear and extends pulley service life
• Herringbone and Diamond Grooves shed water and dirt promoting a self-cleaning effect