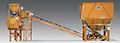
EconoBatch™ Mixer Systems
Compact Plant, Full-size Performance.Designed from the ground up for the way you operate.
You produce medium volume concrete batches. But you still want a high-performing plant. Look no further than EconoBatch™. With capacities up to 48 yards/hour, it’s ideal for a wide range of applications. It can handle up to six aggregates and two cements, and produce consistently high quality wet or dry mixes. Its flexible design means it can be built to your specifications and expanded as you grow. And its economical cost enables you to become profitable quickly. No other plant in its class meets your needs so fully. /Asset/EconoBatch-3.jpg

MP75LAB Lab Concrete Mixer
To meet the need for lab testing of new mix designs and for training in technical centers and universities, the Model MP75 is the elite of the industry. It is a fully functional planetary mixer with all the extra features normally required for application: raise/lower control for mixer top and mixing gear, tipping pan and electric heaters to control mix temperature. The manual control panel includes variable speed control for the mixing action. The mixer is set up for 480 volts 60 Hz. Yield is 1.9 cu. ft., 50 liters. This mixer can create and test mix designs that save you hundreds of thousands of dollars per year in cement costs.
The model MP75LAB mixer has been modified for maximum convenience in lab use.
Features:
• Mixing mechanism and cover with power lift to allow access.
• Filling chute with dust cover.
• Tipping mechanism for raised mixing pan allows whole pan to rotate and discharge into wheelbarrow or trolley .
• Electric pan heaters and temperature sensors to control temperature of mix.
• Variable speed mixing motor.
• Safety guards on all moving parts
• Console type control system for all functions, including motor ammeter
The pan is first cleaned, checked and placed in the horizontal position. The mixing gear is then lowered into position and the test batch is charged through the top-loading chute. Mixing is started and speed controlled by the VFD control. Temperature is controlled with the sensor/heater on the base of the mixer pan. When mixing is complete, the mixing gear is fully raised, allowing the pan to be turned to its tipped position for discharge and cleaning.
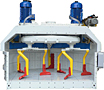
Planetary Countercurrent Concrete Mixers
(11)
The Sicoma high speed planetary / countercurrent concrete mixer is a leader in its class; its design has been refined over many years, from an uncompromising basic design that satisfies the perfectionist to the little touches that you expect from a truly World Class European product.
The planetary (or countercurrent) design has one or two mixing stars that rotate themselves while also rotating around a central point, allowing each arm to cover the whole mixer floor in a number of revolutions. This powerful mixing action is both fast and thorough, resulting in a mixing time, after water is added, of 30 seconds or less for most types of concrete. The result is greater throughput, giving you more concrete per hour for the same size plant, as well as better consistency and greater strength or, on the other hand, a saving on cement. Sicoma's planetary design is superior to turbine and twin-shaft designs for production of all types of dry-cast concrete. The reason for this is its intense mixing action, which breaks up zero-slump mix like nothing else can.
Unlike others of similar design, the paddles and gears are arranged so that every inch of the mixer floor is swept with high repeatability over 60 seconds of operation., each arm sweeping an inch or so behind its previous path and alternate arms covering the gaps so that, even with blades removed from the arms, every particle of concrete would be moved. The consequence is that the mixing action is perfect and the blades do not have to be oversized to do it. Additionally, discharge is fast and complete without the need for a wide scraper tail which creates dead spots in the mixer.
Features:
• Up to 30% greater pan volume than many others rated for the same output, ensuring that it will carry the full rated load and mix it properly.
• Performs equally well on full and small partial batches - the ARMS do the mixing. Paddles are needed for discharge only.
• Large reduction gearbox and oil bath is cool running, good for the life of the mixer. Compare with others using small commercial gear units in tightly cramped, unventilated spaces that can only withstand intermittent duty without overheating and eventual breakdown.
• 5 year / 10,000 hour guarantee on gearboxes.
• Three-armed stars have better mixing action than two-arm and last longer.
• Perfect countercurrent mixing action gives higher strength concrete, saves 10 - 15% cement compared with others.
• Rubber sealed discharge doors run smoothly and eliminate leakage of water.
• Optional additional discharge doors, to 4 maximum.
• Fast and complete cleanout without requiring extra cleanout mechanisms.
• Hydraulic door mechanism gives powerful controllable open/close action.
• Motors and gears rated for occasional startup with full load, without complication of hydraulic coupling.
• Large half-moon cover with optional power lift, giving safe, quick access for cleaning.
• High-security locking cover latch disables startup, ensuring safety even if separate lockout switch is overlooked.
• 15 mm Ni-Hard cast iron liner tiles and mixing blades give 10 times the wear of most other linings.
• Optional Chromium Carbide cladded plates and paddles available at extra cost for extreme wear applications.
• Optional regular steel liner available for low wear applications at reduced cost.
• Best value for money in its class.
• MixTron microwave moisture sensor and controller is fully compatible - perfect for all dry cast mixes.
/Asset/planetary mixers.jpg
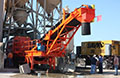
RCC Portable Twin Shaft Mixer
The Portable Twin-Shaft Mixer can turn your dry batch plant into a central mix plant. The Portable Mixer can mix RCC, Paving Mixes and Ready Mix mixes up to 5" slump. Stephens uses a Sicoma (twin shaft mixer) and the trailer was designed to convert any existing dry batch plant into a central mix plant. The mixer can batch over 5 yards of RCC concrete per batch, and it can produce over 200 yards per hour if the dry batch plant can supply the necessary concrete. Stephens can offer hydraulic options for leveling jacks, unfolding conveyor, raise or lower the incline of conveyor and raise/lower the truck collection hopper. The truck collection hopper will allow the mixer to load standard ready mix trucks and/or dump trucks.
8yd and 10yd models are available.
/Asset/Stephens Mfg Portable Twin Shaft Mixer 1.jpg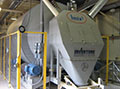
Workhorse Reversing Drum Mixer
(5)Stephens/Inventure Reversing Drum Mixer with a 12.7yard (pr 9.5 m) mixing capacity. ”Runways” of drum are constructed of 1” thick steel. Drum interior, mixing paddles, longitudinal paddles, and charge chute are lined with 1” thick polyurethane, for easy maintenance and cleaning. Discharge shovels are protected with AR 400 plate, discharge chute is lined with ½” polyurethane. The unique paddle arrangement results in higher shear forces within the mixer. Resulting in a shorter mixer cycle, and more efficient use of cementitous materials. Drum liners are in sections to allow front section of mixer drum to be lined sooner than rear section. Drum liners have a million yard or 5 year cost effective, prorated warranty. The paddle liners have a 1 year manufacturer’s warranty.
Charging Chute: Stephens/Inventure Drum has a patented ”swing out” charging chute with a rubber seal. The patented design allow for ”fine tune: adjustments to maintain and keep proper seal between drum and rubber seal. A drip lip and collection hopper help keep the mixer platform area clean from spillage when the ”swing out chute” is in the closed position. A NEW ”scraper blade” has also been added to give a squeegee type action to help keep side of mixer clean. The blade will push water and slurry toward the drip lip and collecting hopper.
Discharge Chute: The mixer drum rotates in one direction for charging and mixing, and reverse rotation for discharging into the truck. This simple system eliminates the costly, high maintenance hydraulic tilt systems that are associated with the tilt mixers. This reversing feature also serves to clean the back of the paddles and prevent the concrete buildup usually associated with the turbulent zone behind the paddles. Discharge pipe will have one section of bolt in A/R liner.
Drive Mechanism: The Stephens/Inventure Drum is resting and rotating on and 4 rubber drums each consisting of 4 solid tires. Stephens tires are 90 durometer, giving added hardness and durability to decipitate heat and give a longer wear life. Many customers experience near 1 million yards before tires need to be replaced. The 4 rubber drums allow for quiet, vibration free and low maintenance operation. This eliminates any steel on steel wear points for the mixer. There are no expensive gears or steel wear points you have to replace. The drums are turned by four shaft mounted speed reducers with V-belt drives and four 50hp electric motors (1800 rpm, TEFC). A variable speed frequency drive controls the speed of the rotation and gives the operator full control of how fast he wants the mixer to discharge. The mixer can temporarily stop or be rotated very slow while waiting for truck to arrive. The slower rotation will give extra time before the concrete activates and begins to set up. Other mixers only operate at one speed and the concrete heats up and activates quicker while inside the drum.
Base frame is designed for easy maintenance and clean up. The frame is designed with an open frame allowing the customer to sweep or wash out under the mixer without having ”boxed in” structural members to hold material or water.
Emergency Drive: Electric emergency drive utilizes two permanently mounted motors with V-belt drive for emptying mixer in case of power failure. Quick hook up will allow customer to disconnect the 50hp belts and connect the two emergency motors. The customer will be required to supply power (generator) to power the emergency drive.
Safety fence: We take safety seriously. To prevent exposure to any points, we provide a full height fencing around the mixer. It is not only the safest fencing in the industry, but it is also very easily removed. Simple undo 4 screws to remove the entire panel, and another 2 screws to remove the post, for full access to the mixer for maintenance.
Electrical Package: The mixer motor control center comes complete with 3rd party label ”UL 508 A” or CSA C22.2 No. 14”. It features a 400 amp 440-480 max volts fused main disconnect supplying a 200hp reversible variable speed controller which controls the speed and direction the mixer is turning. The vari-drive has a load reactor and breaking resistor. the vari-drive feed four 50 hp breaker type overloads which supplies power to the four 50hp mixer motors. Each overload is wired to send a fault signal to the vari-drive stopping all motors in case one motor has a fault condition. The motor control center has ventilation and cooling fans to guard against overheating.
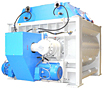
Twin Shaft Concrete Mixers
The Sicoma twin shaft concrete mixer was designed in Italy 20 years ago; it has been refined to give you the outstanding product that you see today. The MAO series heavy duty mixers are the most widely used twin shaft models in the world today; over 6000 in use, worldwide, in ready-mix, precast, block, paver and dam applications. These mixers produce well over 1 million cubic yards of concrete every day. Their compact size allows them to be retrofitted into existing plants, in most cases doubling throughput without the need for two mixers and splitting of material feeds.
The art in concrete mixing is to make a batch of concrete quickly and completely. The MAO's powerful compulsory spiral mixing action throws particles from each side of the mixer towards the center, where they combine; the water is forced through powerful jets into the mix, where it is absorbed completely, allowing the cement slurry to coat all the aggregate particles uniformly, forming the strongest concrete.
Because the mixing occurs in free space above the mixer floor, the wear on the liner plates is very low; the outer 70% of the lined surface is rarely touched by concrete. Only the rows of tiles close to the discharge door will need replacement and you’ll be surprised at how long they last.
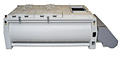
Twin Shaft Continuous (Pug Mill) Concrete Mixers
(5)
The continuous (or 'pug mill') mixer model MAO/C gives a stream of mixed concrete based on volumetric proportioning. Material is fed into one end from two or more aggregate conveyors, cement screw feeder and flow-metered water. The powerful twin-shaft mixing action transforms the raw materials into a continuous stream of mixed concrete suitable for RCC (Roller Compacted Concrete), flowable fill and other less critical high-volume applications.
The MAO/C is smaller and lower in cost than the MAO twin shaft mixer for an equivalent output, per hour.
POWER, SPEED AND RUGGEDNESS
Using the same principle and most of the same components as the MAO twin shaft mixer, the MAO/C continuous mixer is powerful, fast, rugged and requires little maintenance. Its bearings and shaft seals are the same as used in model MAO.
THOROUGH MIXING ACTION
The paddles in the MAO/C mix the concrete while conveying it down the length of the mixer and eventually out of the discharge door at the far end. Mixing is thorough and the resulting product is homogeneous.
SOLID RELIABILITY
Lubrication of the shaft seals is by the same grease pump as used in the MAO. The patented triple seals are good for many years of operation with no maintenance. Bearings and seals have positive separation, to eliminate contamination and wear of the bearing even if the seal should ever leak.