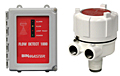
Flow Detect 1000
(2)The BinMaster Flow Detect 1000 consists of two components – the remote sensor probe which is mounted in a pneumatic pipeline, gravity chute or feeder – and the control console which is mounted in an area accessible for users to read the console during operations. The system promotes continuous and efficient operations by informing users that solid or powder materials are flowing and alerts them if the flow status has changed, power has been lost, or if communication between the Remote Sensor Probe and the Control Console has been interrupted.
The FDS 1000 Remote Sensor Probe is a high quality, industrial grade instrument that senses flow / no-flow conditions using Doppler technology (microwave) to provide highly reliable and sensitive motion detection. It works by transmitting a low energy signal through a Teflon process seal into the material flow stream. A portion of the signal is reflected back to the sensor, with the movement of material causing a frequency shift – called the Doppler shift – which is used by the sensor to detect material flow. Unlike the BinMaster Flow Detector 2000, the two-piece model comes with Class II Hazloc approval.
Features:
• Consists of two components including remote sensor and control console
• Uses Doppler technology (microwave) to provide reliable motion detection
• Non-intrusive flush mounting senses through non-metallic surfaces
• Non-contact operation eliminates flow stream interruption and equipment wear
• Control settings can be made without accessing the remote sensor probe
• Fail-safe power protection and loop fault monitor
• “Quick-Set” selectable, single turn calibration
• Hazloc approval Class II
• Alarm for flow/no flow status
• High/low selectable sensitivity adjustment
Specifications:
• Power Requirement: 115 or 230 VAC 50/60 Hz, 5 VA
• Operating Temp Remote: -22°F to +158°F (-30°C to +70°C)
• Operating Temp Console: -31°F to +158°F (-35°C to +70°C)
• Process Temp: 250°F (121°C) if ambient air temperature is below 150°F (65°C)
• Detection Range: Up to 10 feet Frequency: 24.125 GHz, less than 1mW/cm³ (OSHA limit is 10mW/cm³)
• Remote Enclosure: Die cast aluminum
• Remote Approvals: Listed for Class II, Groups E, F & G Hazardous Locations
• Enclosure Type: NEMA 4X, 5, 9 & 12
• Output: DPDT dry contacts, 5A at 240 VAC, or 30 VDC
• Time Delay: Single turn 0.1-15 sec
Applications:
• Senses flow or no-flow conditions of solids and powders in pneumatic pipelines, gravity chutes and feeders
• Virtually unaffected by humidity, ambient light, pressure, vacuum, temperature, noise, vibration, electrical signals, non-metallic buildup or dust
• Used in food processing, plastics, grain, cement, aggregates, paper, mining and many other materials
/Asset/Binmaster flow detect 1000.jpg

Flow Detect 2000
The single-piece flow detector is a flow/no flow detector that, unlike the two-piece flow detector, houses both the remote sensor and control console in a single NEMA 4X enclosure. An important benefit of the Flow Detect 2000 is that it helps prevent cross contamination by ensuring flow has stopped before a new material is introduced into the flow stream. It is ideal for detecting flow conditions of solids and powders in gravity chutes, feeders, pipelines, conveyor belts, or bucket elevators. It is suitable for most industries, including the feed, grain, milling, food, cement, mining, power and plastics industries.
The Flow Detect 2000 uses microwave Doppler technology for highly sensitive motion detection, which is able to pass through non-metallic materials. This provides the device with the ability to 'see through' a plastic pipe, a glass process seal or the wall of a wooden chute to detect the material inside the encasement. It includes a switchable filter which reduces the effect of vibration and ensures the detection of moderate and fast-flowing materials. A single analog relay output communicates flow or no flow status to a PLC and has the option of using both normally open (NO) and normally closed (NC) contacts. LED indicator lights inform the end user of the device's status.
Features:
• Contains the sensing element, power and output connections, and user adjustment controls in a single NEMA 4X enclosure
• Can pass through non-metallic materials
• Easy Installation
• Uses Doppler technology (microwave) to provide reliable motion detection
• Non-intrusive flush mounting senses through non-metallic surfaces
• Non-contact operation eliminates flow stream interruption and equipment wear
• LED lights for flow/no flow status
Applications:
• Used for solids, granules, pellets, meals and powdered materials
• Suitable for most industries, including feed, grain, milling, food, cement, mining, power and plastics