
Model 16-1 Belt Alignment Switch
(4)
This switch is designed especially for bulk material handling conveyor applications. This switch makes sure that belts are aligning properly and prevents costly downtime and unnecessary maintenance costs.

Model BA Belt Alignment Switch
(4)
The Model BA is a heavy-duty conveyor belt mis-alignment switch that either provides an indication or a shut off of the conveyor during a drift condition in order to prevent further damage to the conveyor belt. The output contacts of the Model BA can control up to two separate circuits, one for conveyor shutdown and one for an alarm.
The model BA is relatively inexpensive protection that provides benefit by saving the time, money, and labor associated with replacing a damaged conveyor belt.
Technical Specifications:
• The housing is a heavy welded steel assembly providing long life.
• Rugged 3-1/8" diameter roller with enclosed S.S. ball bearings.
• The unit is mounted on the conveyor by drilling (6) 9/16" diameter holes.
• General purpose (weatherproof) units have (1) 1/2" NPS conduit opening.
• The units have a dry, unpowered micro switch rated for 20A @ 120 VAC, 240 VAC, and 480 VAC.
• An optional breakaway mounting is available, as well as a breakaway mounting with its own independent microswitch.
• The operating temperature range is -40ºF (-40ºC) to 150ºF (65ºC).
• The general-purpose units are rated NEMA 4/5 weatherproof and dust-tight, and explosionproof units are rated NEMA 7/9 for dust ignitionproof and vapor explosion proof.
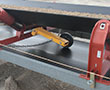
Model BSD Belt Speed Detector
(3)The Model BSD is a "traction action" motion control that indicates when a conveyor belt has slowed or quit moving altogether. The unit can be adjusted as an overspeed, underspeed, or zero speed control. The output of the Model BSD can be wired into a PLC or DCS, or to the optional RMS controller (or MSD controller) which has a DP/DT relay to control up to two separate circuits, one for machinery shutdown and one for an alarm.
The Model BSD can shut down rotating equipment before damage is encountered. It provides protection for interlocked conveyor belts, especially if one of the belts fails due to overloading or quits due to tearing.
ADVANTAGE: No drilling or tapping of tail pulley shaft required, unit is shielded between top and bottom of conveyor belt, and the unit can be placed anywhere on the conveyor belt.
Technical Specifications:
• The controller is sold separately, and is dependent on the sensor chosen.
• The RMS-12S (2 wire) sensor works with the RMS-G series controller, while the MSD-12S3 (3 wire) sensor works with the MSD-800 series controller.
• The RMS-G series controller is available in a NEMA Type 4 polycarbonate housing, while the MSD-800 controller is a panel mount plastic housing with display.
• Both controllers are available in either a 120 VAC, 240 VAC, or 24V AC/DC power input. Specify model number and input voltage upon ordering.
• The sensor can be used in outdoor environments and is connected to the controller(s) with (Belden 8442 or 8760 or similar).
• Each RMS-12S inductive sensor is supplied with 20 feet of electrical cable. Field splice for longer lengths.
• The maximum separation distance between controller and sensor is 200 feet.
• Each controller has a dry, unpowered relay rated for 5A @ 120 VAC, and 240 VAC.
• 6 targets are built into the wheel assembly. Wheel is replaceable if necessary.
• Safety cable is supplied standard, safety chain is optional (additional cost).
• The operating temperature range is -13ºF to 140ºF (-25ºC to 60ºC).
• No drilling or tapping of tail pulley shaft necessary. Mounts between the conveyor belts.
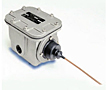
Model DB Damaged Conveyor Belt Detector
(6)
The Model DB is a cable operated damaged belt detector that looks for punctures, tears, or protrusions through the conveyor belt and provides a means of automatic shutdown to limit the amount of damage to the conveyor belt. The output contacts of the Model DB can control up to two separate circuits, one for machinery shutdown and one for an alarm.
The model DB provides substantial cost savings in replacement belting and downtime associated with belt splicing or replacement.
Technical Specifications:
• The housing is cast aluminum, with optional epoxy or polyester coatings available. These coatings will provide protection against corrosion that is equal or greater than cast iron.
• The unit should be used in pairs for best protection of the conveyor belt.
• The unit is mounted on the conveyor by drilling (4) 13/32" diameter holes.
• General purpose (weatherproof) units and explosion proof units have (2) 1" NPT conduit openings.
• The units have (2) dry, unpowered SP/DT micro-switches rated for 20A @ 120 VAC, 240 VAC, and 480 VAC.
• Each unit is supplied with 10 feet of cable, but can be field extended for larger widths.
• Standard operating pull force is 4 lbs; with optional 8 lb. or 16 lb. units available upon request.
• The operating temperature range is -40ºF (-40ºC) to 150ºF (65ºC).
• The general-purpose units are rated NEMA 4/4X weatherproof and corrosion-resistant. Explosionproof units are rated NEMA 7/9 for dust ignitionproof and vapor explosion proof. The dual-rated "D" units are rated NEMA 4 weatherproof and NEMA 9 dust ignitionproof.
• The general-purpose controls are IP65 compliant.
• Most models are UL and c-UL (Canada) listed.
/Asset/CCC Model DB Belt Detector image 2013.jpg

Model SSI Remote Monitoring Module
(3)
The Model SSI is an indication system consisting of 2 separate parts, a Controller-Display module and one or more Field Modules. Together, this system provides an indication which field device has been actuated and allows the operator to concentrate his efforts on one particular unit or location. The Field Module can be installed in any device with a spare N/C (normally closed) contact.
The Status System Indicator provides indication on larger overland conveyor systems which switch or control has been actuated, saving time searching the many units on site.
Technical Specifications:
• The model SSI is a 2 part system consisting of a Controller and a Field Module.
• The MR-2 Controller unit can be powered by 120 VAC or 240 VAC input power.
• The MR-3 Repeater unit (optional) can be powered by 120 VAC or 240 VAC input power.
• The MR-1 field module can be mounted inside any switch or control that has a spare N/C (normally closed) contact.
• The MR-2 Controller has a NEMA 4 (weatherproof) enclosure with a clear polycarbonate cover.
• LCD displays provide easy notification of which Field Module has tripped.
• The maximum separation distance between controller and field module is 6562 feet (2000 m) depending upon number of modules.
• Only 18 ga two conductor shielded twisted pair is required between the Field Modules. Belden 8760 or similar is preferred, Belden 8442 or similar is acceptable.
• The operating temperature range is -40ºF (-40ºC) to 150ºF (65ºC).
• RS-232 output is available on every MR-2 Controller for use as a computer interface

Model TA Belt Alignment Switch
(4)
The Model TA is a belt mis-alignment control that provides an indication when a conveyor belt has drifted off to a dangerous misalignment condition. The output contacts of the Model TA can control up to two separate circuits, one for machinery shutdown and one for an alarm.
The Model TA is relatively inexpensive protection that provides benefit by saving the time, money, and labor associated with replacing a damaged conveyor belt.
Technical Specifications:
• The housing is cast aluminum, with optional epoxy or polyester powder coatings available. These coatings will provide protection against corrosion that is equal or greater than cast iron.
• The roller is a highly visible red epoxy coated roller of 1-1/4" diameter with nylon bushings.
• The unit is mounted on the conveyor by drilling (3) 13/32" diameter holes.
• General purpose (weatherproof) and explosion proof units have (1) 3/4" NPT conduit opening.
• The standard units have dry, unpowered SP/DT microswitch(es) rated for 20A @ 120 VAC, 240VAC, and 480 VAC; 1/2 amp at 125 VDC and 1/4 amp at 250 VDC.
• The roller arm can move up to 90 degrees in either direction. Roller is spring loaded to automatically reset itself. Manual reset available as an option.
• The operating temperature range is -40ºF (-40ºC) to 150ºF (65ºC).
• The general purpose units are rated NEMA 4/4X weatherproof and corrosion-resistant, and NEMA 5 dust-tight. Explosionproof units are rated NEMA 7/9 for dust ignitionproof and vapor explosion proof. The dual-rated "D" units are rated NEMA 4 weatherproof and NEMA 9 dust ignition proof.
• The general purpose controls are IP65 compliant.
• Most models are UL listed and CSA certified.
/Asset/CCC Model TA.jpg
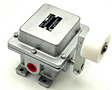
Model TPS Tripper Position Switch
(8)
The Model TA-TPS is a tripper position switch, which is a heavy duty limit switch commonly used to aid in positioning of the "tripper" on a conveyor with multiple discharge points or discharge chutes. The output contacts of the Model TA-TPS can control up to two separate circuits, one for machinery shutdown and one for an alarm.
Technical Specifications:
• The housing is cast aluminum, with optional epoxy or polyester powder coatings available. These coatings will provide protection against corrosion that is equal or greater than cast iron.
• The roller is a heavy duty white acetal material of 3" diameter.
• The unit is mounted on the conveyor by drilling (3) 13/32" diameter holes.
• General purpose (weatherproof) units and explosion proof units have (1) 3/4" NPT conduit opening.
• The units have a dry, unpowered microswitch(es) rated for 20A @ 120 VAC, 240 VAC, and 480 VAC.
• The roller arm can move up to 90 degrees in either direction. Roller is spring loaded to automatically reset itself.
• The operating temperature range is -40ºF (-40ºC) to 150ºF (65ºC).
• The general purpose units are designed NEMA 4/4X weatherproof and corrosion-resistant, and NEMA 5 dust-tight. Explosionproof units are designed NEMA 7/9 for dust ignitionproof and vapor explosion proof. The dual-rated "D" units are designed NEMA 4X weatherproof and NEMA 9 dust ignition proof.
• The general purpose controls are IP65 compliant.
• UL listing and CSA certification is pending

Model VA Bucket Elevator Alignment Control
(2)
The Model VA is the newest belt alignment control specifically designed for use with bucket elevators. The unit is typically used in pairs to provide protection to both sides of the elevator leg, and indicates when the vertical belt strays or drifts beyond acceptable limits. After such time, the unit will trip an output to indicate a problem, or can be used to shut down the leg until inspection and correction is provided.
Technical Specifications:
• The housing is durable sheet metal with a polyester powder coat finish.
• Rugged oversize (3-1/2" diameter) roller with S.S. ball bearings for smooth response.
• The unit is mounted on the bucket elevator by drilling (6) 1/4" diameter holes and a small cut-out.
• Typically used in pairs to provide protection to both sides of the elevator leg.
• General purpose (weatherproof) units and explosion proof units have (1) 3/4" NPT conduit opening.
• The units have a dry, unpowered microswitch rated for 10A @ 120 VAC, 240 VAC, and 480 VAC.
• The operating temperature range is -40ºF (-40ºC) to 150ºF (65ºC).
• The general-purpose units are rated NEMA 4/5 weatherproof and dust-tight, and explosionproof units are rated NEMA 7/9 for dust ignitionproof and vapor explosion proof.
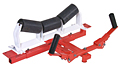
Tracker™ Belt Alignment
(38)The Martin® Tracker™ provides immediate, continuous precision adjustment of wandering conveyor belts. The Tracker™ works where other belt training devices fail to reduce edge damage, prevent spillage and extend belt life.
Features and Benefits:
• Keeps the belt in alignment with automatic, continuous adjustments.
• Improved tracking reduces edge damage, spillage and maintenance expense.
• Continuous precision adjustment of the patented parallel steering/training system keeps the belt tracking properly.
The Martin® Tracker™ is available in 3 models to match the requirements of each application.
• The Tracker™ is designed for applications under typical industrial material handling conditions.
• The Tracker™ HD is designed to withstand the stress associated with wider, thicker belts moving at higher speeds and carrying heavier loads.
• The Tracker™ XHD is engineered to be effective in the most rugged of applications.
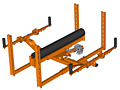
Tracker™ Reversing
(8)The Martin® Tracker™ Reversing provides immediate, continuous, precision adjustment of hard-to-track reversing conveyors. It effectively centers the belt regardless of the direction of travel.
Features and Benefits:
• The Martin® Tracker™ Reversing features sensing rollers and lever arms on both ends of the unit.
• It employs a stainless steel lamella or paddle wheel to sense the direction of belt travel and activate the sensing rollers on the proper end of the unit.
Options:
• Lower Units for installation on the return side.
• Upper Units for the carrying side of conveyors.